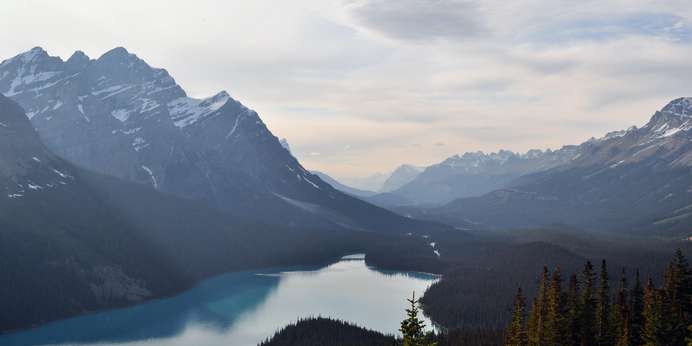
Color Process Automation Technology allows producers of both traditional and alternative plastics to implement environmentally responsible manufacturing practices. Image Source: Tanvi Malik
Plastics are all around us and serve critical functions within virtually every aspect of modern society, from healthcare to telecommunications to transportation to construction. Whether it’s the toothbrush you pick up first thing in the morning, the car you drive to work, or the device on which you are reading at this very moment, plastics shape your ability to care for yourself, communicate with others, and function in daily life. And demand for plastics is expanding; over the past 25 years, plastic production has increased by almost 300%.
In recent years, however, growing concern regarding the environmental impact of plastics has spurred demand for alternative plastic formulation using renewable sources such as methane, corn, and bacteria. Some of these new plastics are now being introduced in mainstream applications. In 2009 Coca-Cola, a major purchaser of plastics, introduced bottles crafted from plastic comprised of up to 30% plant material and in 2010, “Brazilian petrochemical giant Braskem started using ethanol from cane sugar to make a more sustainable polyethylene, one of the most commonly used plastics.”1 While the development of alternative plastics offers exciting possibilities for the future of plastics production, petroleum-based plastic manufacturing currently remains a necessary and invaluable source of plastic products. Now, Color Process Automation Technology, developed through a strategic partnership between HunterLab and Plastore, is making it possible to increase the environmental-friendliness of traditional plastics by heightening efficiency of the manufacturing process itself, which researchers identify a major opportunity for carbon footprint reduction.2
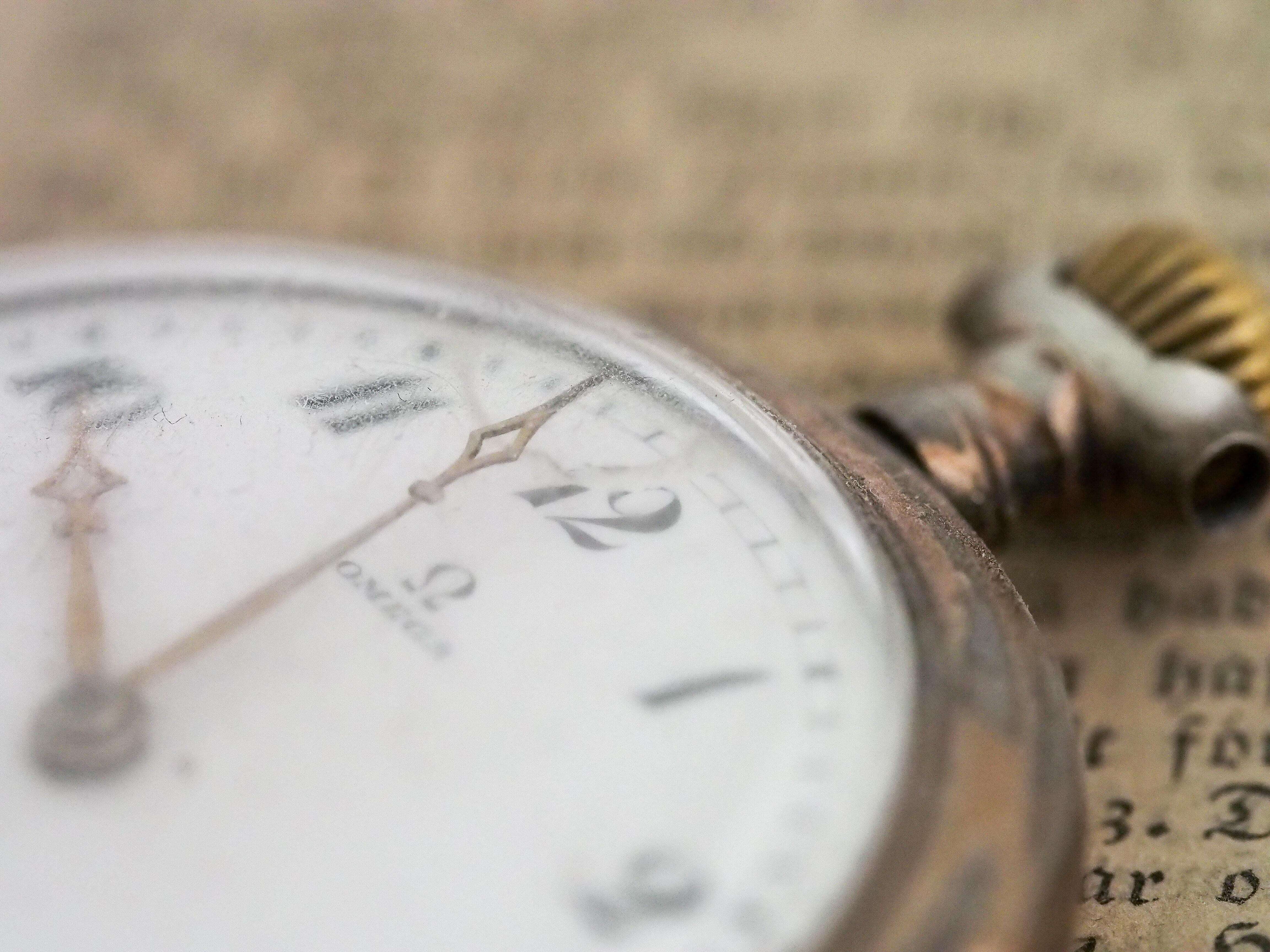
Replacing outdated time-interval based QC practices with continuous, real-time spectrophotometric monitoring can significantly improve efficiency. Image Source: Niklas Rhöse