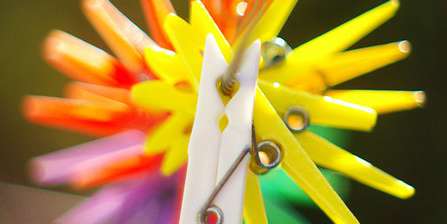
Spectrophotometric technology is critical ensuring accurate color changeover monitoring and optimizing efficiency. Image Source: Flickr user tourist_on_earth
In recent years, manufacturers across industries have had to re-evaluate their production methods to maximize flexibility and efficiency in response to economic uncertainty and rapidly changing consumer tastes. For many, this has meant moving towards a ‘just-in-time’ manufacturing methodology. First conceptualized in Japan in the 1960s, the JIT philosophy has become increasingly popular in the West as it allows manufacturers to minimize inventory levels and only receive materials as they are needed, reducing waste and facilitating responsiveness to evolving market demands.1 For plastic product manufacturers, increasing color changeover frequency has been a major part of the switch to JIT production and spectrophotometers are playing an integral role in developing more efficient changeover methods.
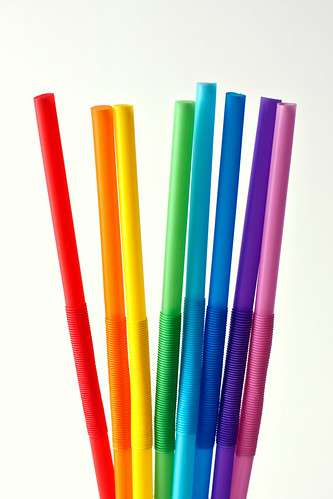
Whereas plastic manufacturers used to run a single color for days at a time, today it is common to see multiple changeovers in a single shift. Image Source: Flickr user Horia Varlan