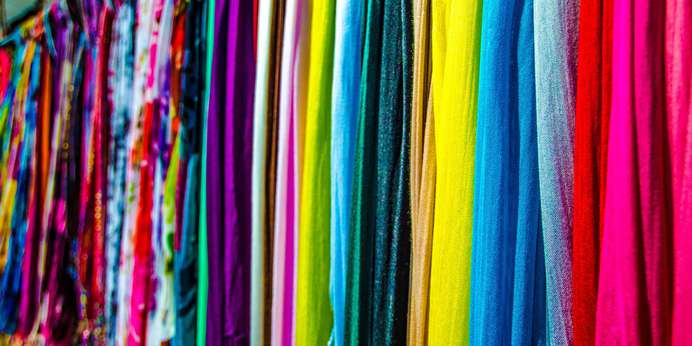
By 3:00 am, it’s already on Twitter. At 7:00 the phone is ringing, and the morning just got hectic. Your primary cotton source, a Vietnamese plantation, lost its storage facilities and much of its crop to a major mudslide. Nobody was hurt, but you’ve got to find a new supplier to have any hope of completing the orders already in your pipeline.
That’s no problem. Saved in your files is a three-page list of cotton suppliers, from New Zealand to Spain. A quick look and you find a Turkish plantation that can ship bales down the Mediterranean and across the Atlantic, without a significant price difference. But it’s too bad—you’ve been buying from the same company for years, and you already know that the Turkish cotton will require you to adjust your dyeing process.
It’s not exactly a secret that color consistency can be affected by any change in the location in which a fiber is grown, made, or dyed.1 And if garment manufacturers have more opportunities than ever in a global marketplace, they also have more competition—should you deliver a late or unsatisfactory order, there is always another manufacturer eager to step in and demonstrate their reliability. Every time you lose productivity because of color discrepancies, you risk losing business.
Spectrophotometers Increase Lab Dye Efficiency
But objective color measurement is achievable with spectrophotometric technology. Samples of incoming fabric shipments from suppliers can be scanned and their color assigned an objective numerical value using the Hunter l*a*b coordinate system.
Knowing the color of a fabric before it enters the lab for dyeing allows you to save time by reducing trial-and-error waste. Previous dips might yield information on how a given fabric—Moroccan wool, for example—reacts with specific dyes. Access to this data allows you to more accurately predict which dyes will render a color to match your standard. And by positively identifying that an incoming fabric sample is exactly the same color as a previous sample, you can produce a standard-matching dye in very few trials.
By systematically reducing color disagreement with spectrophotometric analysis, the number of lab dye cycles can be reduced, opening up days or weeks in your lab dye schedule—and perhaps even allowing you to take on a larger volume of orders.
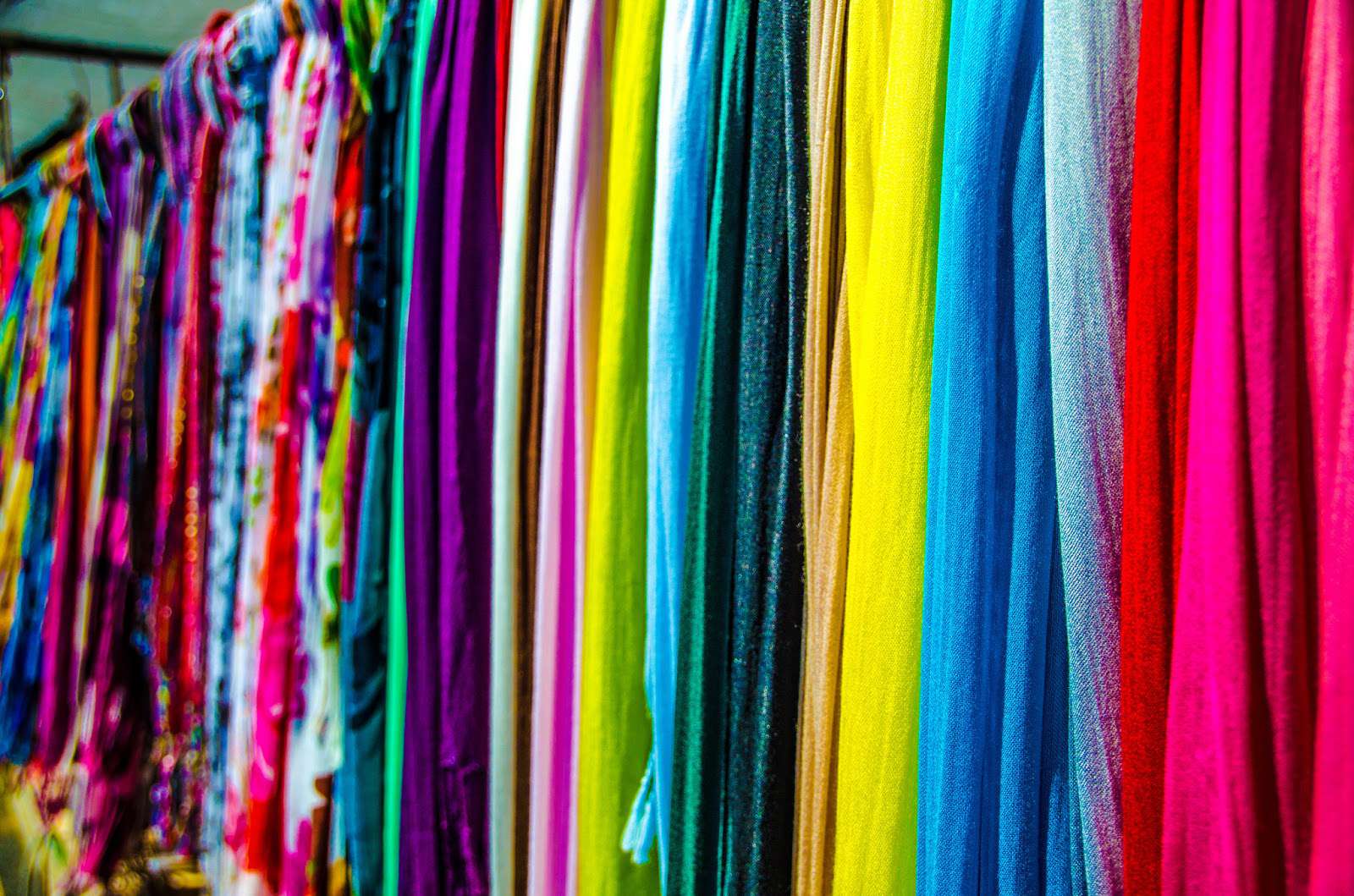
The dyeing process is made easier by having data from previous batches on hand. Image credit: Flickr user Kevin Jarrett (CC BY 2.0)