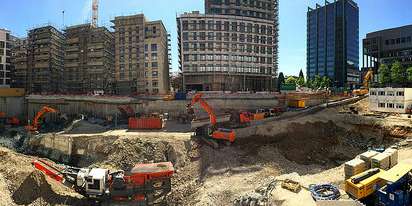
For the second time, the test slab you’ve mixed has turned out a different color than what the architect approved, and for the second time you’ve had to delay construction. The engineer is getting sick of recasting tests. The architect is getting sick of having to come down to the site again and again. Workers are sitting idle, and you’ve got egg on your face. You’ve been using the same mix every time—so what’s the problem? How can you stop this from happening?
Slight changes in the cementitious materials used in your mix can, of course, result in color variation that exceeds established tolerances. Gravel, aggregate, and additives from different suppliers will produce differently colored slabs, as will variations in your water to cement ratio. But even when all of this is controlled for, improper measurement can cause your team to misidentify sample colors—leading otherwise acceptable results to fail.
Color Delays Cost in Construction
And these failures don’t come cheaply. To ensure that, by the time you need to pour concrete, you know exactly what to pour, sample testing of field batches already needs to be conducted at least a month1 prior to construction. But as any project manager knows, plans unravel easily. Between the need to prepare samples for each separate color, the logistics of coordinating architects’ and engineers’ schedules, and the lead time required for each test, problems with sample slabs can easily delay the initial pour.
Time lost is money wasted on labor and materials, of course, but repeated failures to produce the color specified in your contract can also result in legal squabbles2 with architects, project managers, or building owners. Even a successful lawsuit can damage reputations and cause contractors to lose potential business. Bad news travels quickly.
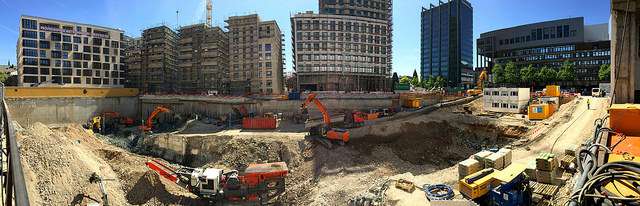
Color standard delays can cost time and money. Image credit: Flickr User Mikkal Noptek (CC BY 2.0)